22.11.2022
Applications of bio-nano materials: update on the BIOMAC Test Cases
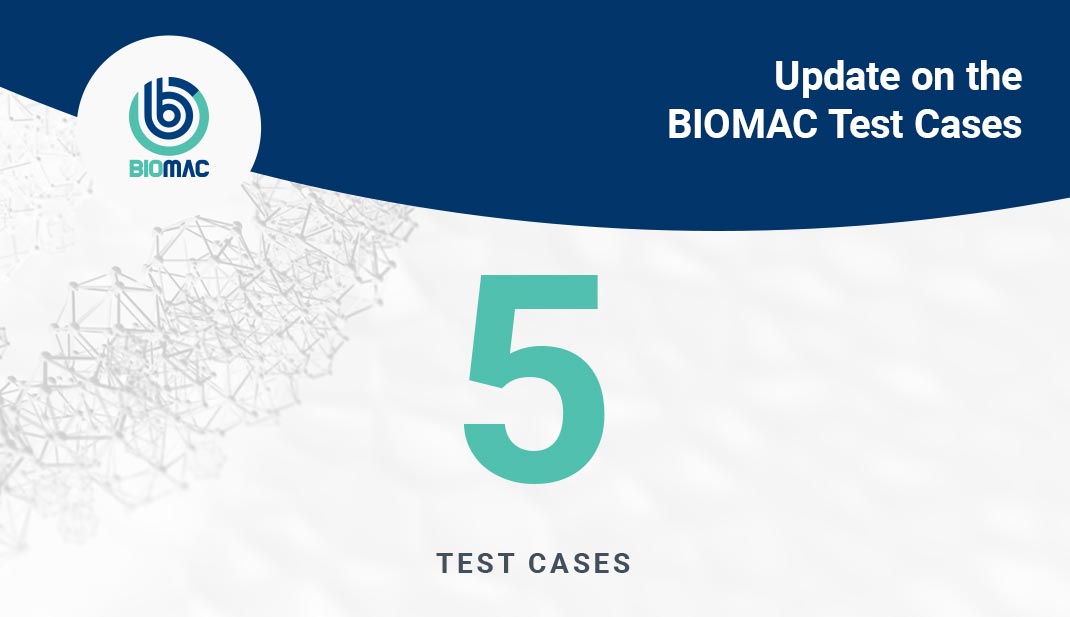
To ensure the validation of the BIOMAC concept, 5 Test Cases (TeCs) are meant to demonstrate the feasibility of realizing specific products by making use of the Pilot Lines developed in the Project. Here we are presenting a short overview and update on the status of the Test Cases.
Test Case 1 - Automotive
TeC1 is about the formation of automotive components for interior applications through a photopolymerization-based additive manufacturing process. DIAD selected the Italian company DIGRO to carry out the Automotive components’ demonstrator.
DIGRO carried out a series of SLS printing trials using a bio - resin PLA to check the feasibility of the component by additive manufacturing. With respect to the PLA based filament used in the FDM technique the PLA resins have higher thermal stability and longer durability and can represent an excellent comparison with respect to BIOMAC bio - based materials. Once assessed the feasibility of the component by AM, DIGRO provided AIMEN (another BIOMAC partner) with the CAD of the component to be uploaded in the control system of AIMEN AM equipment.
At present, several experimentations are on - going with different compositions elaborated by Fraunhofer Institute for Wood Research Wilhelm-Klauditz-Institut (FH-WKI), specialist in bio - based materials.All the compositions tested reach a percentage of bio - component equal to 85% and AIMEN test for printability confirmed that the level of viscosity achieved is functional to the requirement of the equipment used, shown in the following picture. AIMEN AM machine is based on Two Photon Polymerization and, through this machine, will be realised the first prototype of sun - visor with bio – based polyesther resins.
Figure 1 AIMEN AM 2P2 Equipment
Test Case 2 – Agriculture
TeC2 provides biobased solutions for agricultural applications, with specific focus on mulching and grow pots.
Mulching is a consolidated agronomic technique used to prevent weed growth, to increase soil temperature (anticipating crop development) and preserving soil moisture. Mulch films are usually made by a coloured layer of plastics in order to block UV lights to favour selected crop growth reducing sun light competition related to weed development. Novamont is leader in the production of bioplastics, including those used for the production of biodegradable in soil mulch films, certified according to European standard EN17033.
Another application in this test case relates to the production of Biodegradable stackable grow pots. Plastic made grow pots are widely used in home gardens, plant nurseries and commercial farms, however their disposal and recycling is problematic. In the TeC2, BIOMAC demonstrates the advantage of biodegradable grow pots.
Figure 3 Mulching films on the ground
Figure 2.1 Biodegradable grow pots
Test Case 3 – Food packaging
This Test Case focusses on the production of a new of food packaging materials. In particular, it has led to the production of
- Biocompostable and biodegradable food containers, using biobased PLA foils, reinforced with nano-additives to enhance the mechanical and antibacterial properties of flexible packaging materials. This material shows also improved characteristics for food maintenance/conservation and safety
Nanofibrillated cellulose (NFC) from cellulosic pulp has been produced using a continuous mechanical disintegration process. In order to produce different qualities of the NFC, the cellulosic pulp was bleached previously to the disintegration.
Figure 4 NFC from cellulosic pulp
Figure 5 NFC from bleached cellulosic pulp
These NFC were modified in order to improve the compatibility with the polymeric matrix, polylactic acid (PLA). Also, the modified NFCs will be evaluated as an additive to develop PLA based masterbatches. On the other hand, NFCs produced will be used to formulate different barrier coating which will be used to improve the barrier of the based PLA films.
The PLA nanocomposites were developed via “in-situ” polymerization by ROP of Lactide with Bacterial nanocellulose, Nanofibrillated Cellulose, Nanolignin and Biochar as functional additives that have been obtained in different pilot lines of BIOMAC. These materials were obtained at lab scale to study the reactivity and influence of the nanoparticles in the ROP of lactide.
Figure 6 PLA with NFCs obtained
Once PLA and PLA copolymer nanocomposites formulations are developed at lab scale, they will be scaled up in a continuous reactive extrusion and/or compounding process at pilot plant scale.
The PLA will be used for obtaining films with a transparent colour. This product will be produced with material 100% biodegradable and compostable according to EN 13432 standard.
Figure 7 Example of food packaging made from biodegradable polymers
Test Case 4 - Construction
BIOMAC partners are currently testing the use of Bio-nanocomposites sandwich panels in the construction industry.
The main outstanding feature of sandwich panels comes from their composition. They consist of an inner core generally composed of rigid polyurethane (PUR) or polyisocyanurate (PIR) foams, protected by two thin sheets of steel or composite material that give the panel a very low weight.
By applying a printable thermoplastic and fiberglass sheets, it is possible to industrialize the production of sandwich panels with complex geometries, thus achieving greater cost efficiency and allowing sandwich panels to be used in structural elements of variable geometry that have generally been restricted to other materials in the sector, such as concrete, steel or timber.
Figure 8 3D printed footbridge using sandwich panels (1)
Figure 9 3D printed footbridge using sandwich panels (2)
Figure 10 Complex formwork on a pedestrian footbridge over the Manzanares river
Test Case 5 – Printed electronics
TeC5 aims at developing compositions and processes for embedding stretchable conductive materials into textiles, to be used for wearable electronics.
The development of such materials will be done via printing processes, using bio-based stretchable substrates, inks, and adhesives. Bio-based inks will be developed with bio-resins and functionalized CNC and BNC nanobiofillers.
To make the inks electrically conducting, conductive elements will be added. Several materials will be tested in this context, potentially including biochar, biochar modified with silver nanoparticles, silver.
Detail of the werable device