15.06.2023
Unlocking the Potential: Exploring Diverse Applications of Lignin
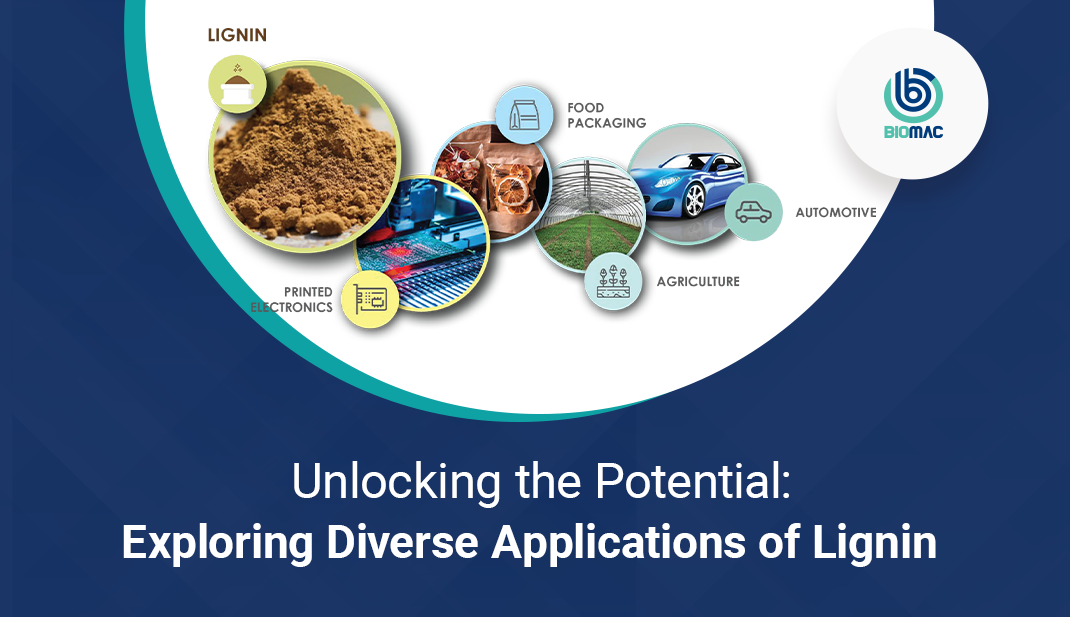
Lignin is the second most abundant biopolymer after cellulose with an approximate annual production of 100 million metric tons per year.1 Being a by-product of the paper and pulp industry, most of this biomaterial gets incinerated to produce steam for process energy. In the past few decades however, due to its low cost and natural abundance as a renewable organic carbon source, the potential it has in numerous applications as a raw material for valuable products is being unraveled.2
Raw lignin is a collection of highly heterogenous polymers derived primarily from three different monomers: coniferyl alcohol, sinapyl alcohol and paracoumaryl alcohol which are diversely cross-linked. The relative amounts of monomers vary greatly depending on the plant source and on the different pulping processes employed, multiple structural variations exist making chemical analysis and standardization challenging. Generally, there are four main types of lignin resulting from the extraction process used: The sulfur containing processes include Kraft lignin and lignosulfonate and sulfur-free processes to obtain Organosolv lignin and Soda lignin. These technical lignins may then be utilized as macro-polymers or further processed to depolymerize lignin into lower weight monomers and/or subjected to further chemical modifications depending on the intended application.
Although significant research has been conducted on lignin’s potential utility in numerous materials and applications, these have not yet to reached industrial production and are currently limited to low value applications which is mainly due to lignin’s structural complexity. In this article a few of these applications will be briefly discussed.
Figure 1: Industrial applications of lignin.
The use of lignin in construction materials is of increasing interest, more specifically in cement composites since most of the additives and admixtures currently used are derived from crude oil as the starting material. For example, current research shows that rigid polyurethane foams (RPUFs) containing lignin exhibit similar properties to commercial petroleum derived products.3 The production of more environmentally friendly corrosion inhibitors and protective coatings is becoming more feasible with the introduction of lignin in these materials. Cost and environmental concerns are also driving the replacement of bitumen in asphalt with lignin. The increase of the use of lignin in construction will have a double benefit: first, it will increase the level of sustainability in construction, and second, it will contribute to finding new applications with high added value for lignin.
Another study related to the incorporation of lignin onto poly(lactic acid) (PLA) for the application of food packaging materials revealed interesting results. Various amounts of lignin microparticles (LMP) were melt blended with neat PLA and ethylene-vinyl acetate-glycidyl methacrylate (NPG) to prepare different PLA composite films that were subjected to selected tests and studies. Mechanical test results show that the addition of LMP-g-PLA made a significant contribution to the toughness of PLA/NPG blend, as the elongation at break increased up to 236% in PLA/NPG/1LMP sample.4 Furthermore, UV–Vis spectroscopy results showed that PLA/NPG/LMP films have excellent UV resistance behavior without sacrificing too much the transparency. Results from overall migration and antioxidant tests confirmed that PLA films blended with NPG and LMP-g-PLA can be used as competitive materials in active food packaging industry.
Another area where lignin finds is use is that of printed electronics. Printed wire boards formulations prepared from 50% lignin combined with standard epoxy-based resins demonstrated intractable crosslinked resins that met the bulk of physical and electrical requirements.5 The resin system was designed to be processed on current manufacturing equipment, which was demonstrated by fabrication of test vehicles in the normal FR4 processing line in IBM’s facilities. When subjecting these fabricated boards to the accelerated thermal cycle (ATC) and temperature, humidity, and bias (THB) stress tests they showed excellent results. Additionally, the lignin/epoxy formulations have potential financial incentives (dependent on the lignin’s source and any required purification) that would increase their desirability. Printed wiring boards are a mature market operating on relatively small profit margins, hence a resin that offers financial savings should be particularly appealing. A life-cycle assessment indicated that the lignin/epoxy resin has environmental advantages in terms of energy usage, solid wastes, and air- and waterborne emissions, especially those responsible for global warming such as CO2 from fossil sources, methane, and nitrogen oxides. Due to the lower energy requirements for production of natural raw materials, fuel usage for resin production and manufacture may be cut by as much as 40% by converting from standard FR4 to lignin-based resins.
In agriculture lignin can be useful as a plant growth regulator, a pesticide as well as a soil improver.6 In a similar manner to plant hormones that promote growth and development of plants, lignin’s complex structure has the same effect. Using lignin from black liquor or by directly using black liquor from the pulping process to prepare reagents with a concentration of 10-4 showed improved survival rate and growth rate of seedlings after transplant. Soaked seedling roots in the aforementioned solution for 15 h increased the survival rate of spruce and pine seedlings to a large extent compared to the corresponding control solution containing no lignin.
Additionally, lignin, with its inherent strength and high carbon content, is an attractive choice for automotive materials. It can be processed into various forms, such as lignin nanoparticles and lignin-based composites, which are utilized in lightweight panels, foams, elastomers, adhesives, and coatings for automotive components. The most common application is the integration of lignin into polyurethane (PU) products. The addition of lignin in rigid PU foams enhances their properties compared to conventional foams, including increased crosslinking density, improved biodegradability, greater antioxidant characteristics, enhanced UV and thermal stability, and improved mechanical properties. Furthermore, lignin can replace traditional plastic phases in thermoplastics and thermoplastic elastomers, offering sustainable advantages. By using lignin-based materials, the automotive industry can reduce the environmental impact of manufacturing processes, enhance fuel efficiency through weight reduction, and improve overall sustainability.
Finally, other inclined industrial uses of lignin include textile, reinforcement, binder, adhesive, fuel, emulsifier and stabilizer, dispersant and agricultural applications. Although much more research is required for commercialization of these applications, lignin has unlimited potential to be used as an environmentally friendly bio-based and biodegradable material.
_________________________
[1]
Ind. Crop. Prod., 2019, 139, 111526.
[2]
J. Chem. Rev., 2023, 5(1), 56.
[3]
Intern. J. of Bio. Macrom., 2021, 187, 624.
[4]
Intern. J. of Bio. Macrom., 2020, 144, 102.
[5]
J. of Indu. Eco. 2000, 4, 93
[6]
Industrial Crops and Products, 2021, 170, 113646