8.02.2023
Nanocellulose as a filler in polymer composites
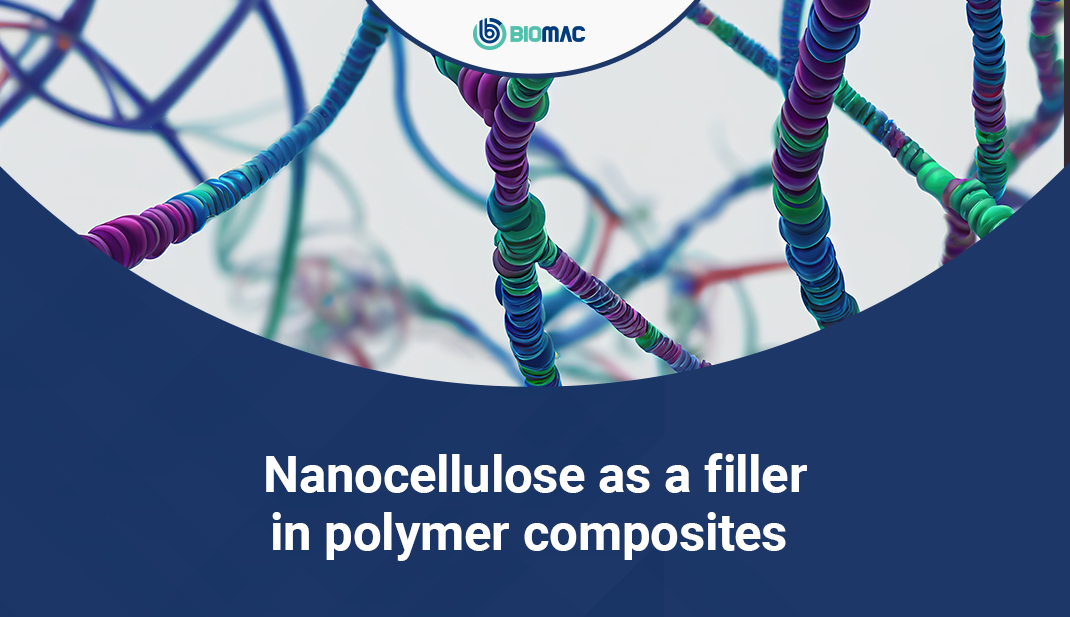
Cellulose is the main substance of a plant’s cell walls, helping plants to remain stiff and upright, thus, it can be extracted from plant sources, agriculture waste, animals, and bacterial pellicle. [1] Nanocellulosic materials have recently gained significant research interest as potential nanofiller for the reinforcements in the polymer matrices due to its renewable in nature, inexpensive, excellent physical properties readily availability, biocompatibility, tailorable surface properties.[2]
Figure 1. PVA composites reinforced with nanocellulose
Why chose NANO-cellulose?
Scientists extract nanocellulose from various natural resources, such as cotton, jute, ramie, bamboo, rice husk, starch, sisal, etc., and use them for the advanced material applications. Nanocelluloses combine the important chemical properties of cellulose with interesting phenomena of nanoscale materials.
Nanocellulose possesses low density, high aspect ratio, impressive mechanical properties, nanoscale dimensions, which shows huge potential applications as a reinforced filler.[4] Nanosized cellulosic materials can improve the overall performance of nanocomposites, in terms of mechanical properties and other functional properties viz. partial degradation, improvement of barrier properties, etc.).
Figure 2. The hierarchical structure of cellulose fiber permits its degradation into nano scale particles. [3]
Νanocelluloses have the potential to reinforce various polymer matrices with very low filler loadings to achieve targeted properties. Cellulosic nanofillers are used for the reinforcement of thermoplastic polymers. Applications of nanocellulose reinforced nanocomposites could be considered for the potential in diverse fields, such as in packaging products, construction, automotive, furniture, electronics, membranes, etc.[2]α
Properties of nanocellulose reinforced polymers
The addition of nanocellulose leads to improvement in overall performance of polymer composites by improving their mechanical, thermal and barrier properties, usually even at very low content.
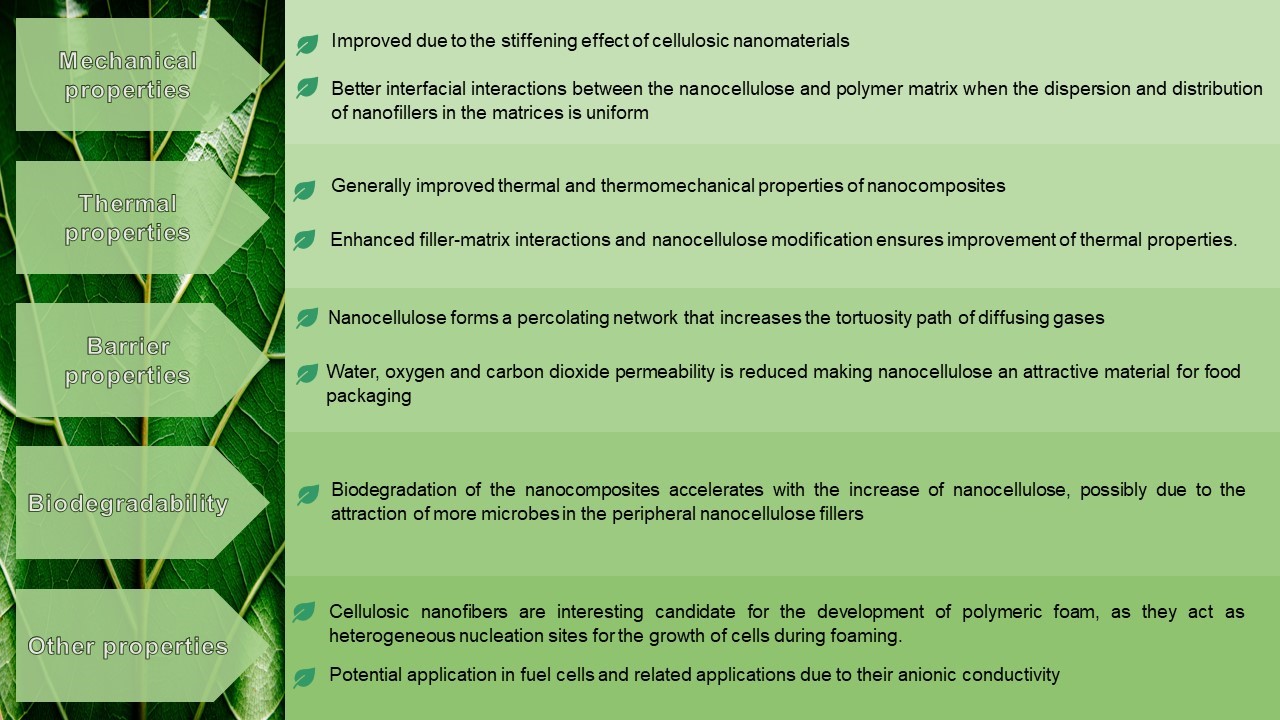
Commercial Aspects
Since biobased polymers reinforced by nanocellulose can reach the properties of fossil-derived polymers, the cost of the expensive petroleum resource and energy consumed to derive petrobased plastic could be saved, making cellulose composites relatively cheaper. Cellulosic nanomaterials remain expensive due to the high cost of production. In addition, high moisture content inevitably accompanying the production of nanocellulose is a problem. It is undeniable that the solvent substitution step also leads to an increase in cost. The supply system of nanocellulose is being established in countries where its research is precedent. By analogy with general theory, cost reductions can be expected by large-scale production. In order to reach large-scale production, exploitation of application is important. For that, we need to pursue what we cannot do without nanocellulose. In addition to designing attractive composites in terms of functionality and performance, further brush-ups are required to streamline the process of compounding. [5] Via the BIOMAC OITB, companies have the opportunity to develop and upscale new materials with nanocellulose at a competitive cost, taking advantage of the expertise of the BIOMAC ecosystem partners.
The utilization of nanocellulose in the BIOMAC project
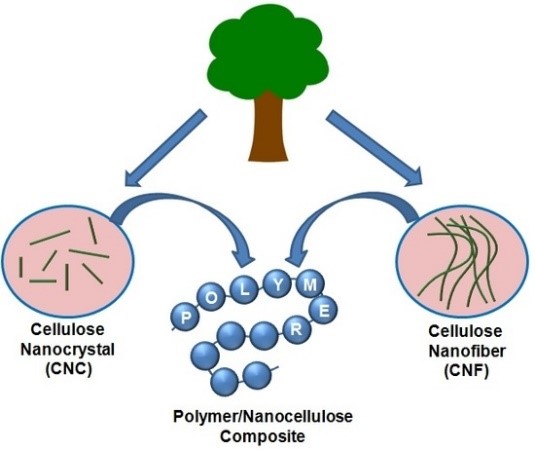
Figure 3: Schematic representation of polymers reinforced with nanocellulose. [5]
The produced nanocellulose is added in polymeric materials to enhance their mechanical and barrier properties. Bio-based resins reinforced with nanocellulose will be used in the fabrication of interior car parts and components for the automotive industry. For food packaging applications, nanocellulose will be added in PLA-based films to improve their barrier properties. Last but not least, nanocellulose in isocyanate free TPU biopolymers will improve their mechanical properties, reduce the weight and cost, and will be validated in construction applications.
If you want to take advantage of the great properties of nanocellulose as a filler in polymer-based composites, regardless of the final applications, contact the team of BIOMAC at
biomac@chem.auth.gr and we might be able to help you with developing and upscaling your product concept!
References
[1]
Omran, A. A. B.; Mohammed, A. A. B. A.; Sapuan, S. M.; Ilyas, R. A.; Asyraf, M. R. M.; Koloor, S. S. R.; Petrů, M. Micro-and Nanocellulose in Polymer Composite Materials: A Review. Polymers (Basel). 2021, 13 (2), 1–30. https://doi.org/10.3390/polym13020231.
[2]
Mondal, S. Review on Nanocellulose Polymer Nanocomposites. Polym. - Plast. Technol. Eng. 2018, 57 (13), 1377–1391. https://doi.org/10.1080/03602559.2017.1381253.
[3]
Alonso-Lerma, B.; Barandiaran, L.; Ugarte, L.; Larraza, I.; Reifs, A.; Olmos-Juste, R.; Barruetabeña, N.; Amenabar, I.; Hillenbrand, R.; Eceiza, A.; Perez-Jimenez, R. High Performance Crystalline Nanocellulose Using an Ancestral Endoglucanase. Commun. Mater. 2020, 1 (1). https://doi.org/10.1038/s43246-020-00055-5.
[4]
Hao, W.; Wang, M.; Zhou, F.; Luo, H.; Xie, X.; Luo, F.; Cha, R. A Review on Nanocellulose as a Lightweight Filler of Polyolefin Composites. Carbohydr. Polym. 2020, 243 (May). https://doi.org/10.1016/j.carbpol.2020.116466.
[5]
Chakrabarty, A.; Teramoto, Y. Recent Advances in Nanocellulose Composites with Polymers: A Guide for Choosing Partners and How to Incorporate Them. Polymers (Basel). 2018, 10 (5). https://doi.org/10.3390/polym10050517.
[6]
Reddy, J. P.; Rhim, J. W. Characterization of Bionanocomposite Films Prepared with Agar and Paper-Mulberry Pulp Nanocellulose. Carbohydr. Polym. 2014, 110, 480–488. https://doi.org/10.1016/j.carbpol.2014.04.056.
[7]
Michelin, M.; Gomes, D. G.; Romaní, A.; Polizeli, M. de L. T. M.; Teixeira, J. A. Nanocellulose Production: Exploring the Enzymatic Route and Residues of Pulp and Paper Industry. Molecules 2020, 25 (15), 1–36. https://doi.org/10.3390/molecules25153411.
[8]
Li, W.; Wu, Q.; Zhao, X.; Huang, Z.; Cao, J.; Li, J.; Liu, S. Enhanced Thermal and Mechanical Properties of PVA Composites Formed with Filamentous Nanocellulose Fibrils. Carbohydr. Polym. 2014, 113, 403–410. https://doi.org/10.1016/j.carbpol.2014.07.031.
[9]
Lani, N. S.; Ngadi, N.; Johari, A.; Jusoh, M. Isolation, Characterization, and Application of Nanocellulose from Oil Palm Empty Fruit Bunch Fiber as Nanocomposites. J. Nanomater. 2014, 2014. https://doi.org/10.1155/2014/702538.
[10]
Abraham, E.; Elbi, P. A.; Deepa, B.; Jyotishkumar, P.; Pothen, L. A.; Narine, S. S.; Thomas, S. X-Ray Diffraction and Biodegradation Analysis of Green Composites of Natural Rubber/Nanocellulose. Polym. Degrad. Stab. 2012, 97 (11), 2378–2387. https://doi.org/10.1016/j.polymdegradstab.2012.07.028.
[11]
Trifol, J.; Plackett, D.; Sillard, C.; Szabo, P.; Bras, J.; Daugaard, A. E. Hybrid Poly(Lactic Acid)/Nanocellulose/Nanoclay Composites with Synergistically Enhanced Barrier Properties and Improved Thermomechanical Resistance. Polym. Int. 2016, 65 (8), 988–995. https://doi.org/10.1002/pi.5154.
[12]
Zimmermann, M. V. G.; da Silva, M. P.; Zattera, A. J.; Campomanes Santana, R. M. Effect of Nanocellulose Fibers and Acetylated Nanocellulose Fibers on Properties of Poly(Ethylene-Co-Vinyl Acetate) Foams. J. Appl. Polym. Sci. 2017, 134 (17), 1–12. https://doi.org/10.1002/app.44760.
[13]
Vilela, C.; Sousa, N.; Pinto, R. J. B.; Silvestre, A. J. D.; Figueiredo, F. M. L.; Freire, C. S. R. Exploiting Poly(Ionic Liquids) and Nanocellulose for the Development of Bio-Based Anion-Exchange Membranes. Biomass and Bioenergy 2017, 100, 116–125. https://doi.org/10.1016/j.biombioe.2017.03.016.